View technical ceramics related powders & slurries
What is a technical ceramic?
The expression “Technical ceramics” covers plenty of applications, such as :
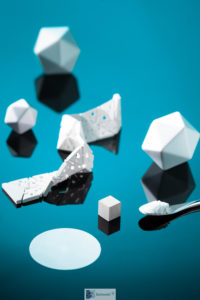
- Ceramic coating: Protecting, reinforcing another material
- Cutting tools: Cutting hard materials
- Thermal management ceramics : Insulating or conducting heat: thermal management ceramics
- Ceramic membranes for ultrafiltration: Filtering
Ceramic coating properties
Coatings are designed to bring new properties to the coated material. It allows a functionalizing of the material. The ceramic coating must have various properties depending on the targeted function:
- Flatness: We control the particle size of our powders, which optimizes the thickness of the layer.
- Resistance to chemical products: coatings made of high purity alumina or special oxides are intrinsically lowly reactive to chemical stress. We also control the surface chemistry of the particles to enhance chemical resistance.
- Resistance to mechanical stress: this is an intrinsic properties of fine oxides particles leading to a fine microstructure.
- Control of other physical properties, such as wettability or porosity. For instance, we can optimize the porosity by controlling the size of the particles and the distribution of size.
- Sintering temperature below the coated material’s: we produce highly reactive particles in order to make it possible, by controlling the chemical purity of our products. Moreover, we control the shrinkage of the material in order to maximize the compatibility of the coating slurry and the coated material.
All these controlled properties of our products are helping to control rheology (especially viscosity) of the final coating slurry.
Ceramic coating is often used for sensors, such as oxygen sensors. The coating protects the sensor from corrosion.
Cutting tools properties
Ceramic cutting tools can become necessary when cutting temperature is high and no coolant comes in. Cutting tools in ceramic, made of High Purity Alumina (HPA), are targeting:
- Thermal and chemical stablility (avoid oxidation). This is an intrinsic property of an HPA ceramic.
- Wear resistance. Only high-density pieces with high intrinsic hardness and no porosity can provide a very good resistance to wear. We provide HPA and Zirconia with controlled agglomerates (which tend to zero for no porosity) and controlled particle size and particle size distribution.
- Fracture toughness. Furthermore, the finer the microstructure, the tougher the cutting tool. Baikowski® provides HPA & Zirconia guaranteeing controlled size of the final ceramic grains and hardness due to the finest microstructure.
We control our products in particle size, particle size distribution and agglomerates. All those properties enable to control the sintering reactivity. The ceramic obtained by sintering our powders is highly dense at a low temperature. We can also add various dopants, in order to foster the densification of the ceramic. Moreover, some additives can reinforce the mechanical properties, like zirconia.
View cutting tools related powders & slurries
Technical ceramics for thermal management
The design of some ceramic pieces expands properties such as insulation or diffusion. For example, this is the case for small ceramic pieces in electronics, which act as heat sinks into the device. This function is gaining importance, insofar as electronic devices go more and more downsizing and functionalizing. Thermal management ceramics are meant to be:
- Cooling or heat exchanging efficiently and in a long-lasting way. This is an essential advantage of technical ceramics compared to metal. It guarantees low maintenance costs thanks to its superior chemical durability. Baikowski® provides high purity alumina enabling to control the final porosity of the ceramic. Indeed, we control the particle size, particle size distribution & agglomerates in our products. It participates in the efficiency of the heat dissipation or insulation.
- Lightweight, due to the design evolution of the electronic devices. Our products allow to make efficient thermal management ceramics at a low thickness, thanks to the control of sintering reactivity and shrinkage.
If thermal management is made with a high purity alumina-based paste, our products enable to obtain a controlled viscosity thanks to the control of the particle size, particle size distribution & surface functionalization.
View our thermal management offering
Technical ceramics for ultrafiltration
Our products can be used in other technical ceramics applications such as ultrafiltration. For example, our products allow to develop hierarchical porosity in ultrafiltration ceramics. This functionality implies that the customer will use specific processes to manage such a high level of control of the porosity of the final ceramic membrane.
We can adapt our offer according to the process of each customer, either they are looking for macroporosity or nanoporosity ceramic powder. For example, we design high purity alumina for mesoporous membranes such as plate and frame ceramic membranes. These ceramic membranes use mesoporosity to filter water and thus operating H2O cleaning.
View filtration related powders & slurries
High Purity Alumina in the battery
The experts are using high purity alumina (HPA) for its key input on separator stability in lithium-ion batteries.
HPA is chemically inert vis-à-vis lithium and electrolyte components. Baikowski® processes guarantee chemical purity and surface properties control, which minimize the impact of the HPA on the battery parts.
A controlled architecture of the particles stacking ensures the dimensional stability of the HPA coated polymeric separator. We guarantee optimal control of our products morphology in order to ensure the best dimensional stability with the lowest thickness. Our mission, the textural design, is to make you reach the best compromise between technology and cost-efficiency for a successful separator coating.
We provide HPA with high specific surface area, adapted to cathode material coating, such as CR125.
As technologies evolve, HPA has a role to play in overcoming the limitations such as for solid-state batteries. Itcan be used as a separator to prevent the contact between anode and catode, as well as to enhance the electrolytes ionic conductivity and electrochemical performance.
Find further information in our